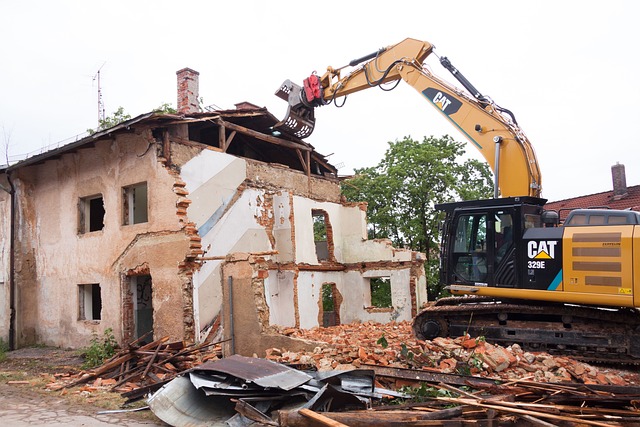
The Reuse of Wood Products Left after Demolition: Challenges, Facilitation and Green Public Procurement’s Role—Helsinki’s City Experience
Keywords: reuse of wood products, Green Public Procurement (GPP), Construction Product Regulation (CPR), Waste Framework Directive (WFD), EU Taxonomy, method for assessment
Introduction
The construction industry plays a significant role in the world economy while also being among the major sectors that contribute to environmental degradation and resource scarcity. In the European Union, up to 17 % of the GDP is spent on annual public procurement, including purchases in the construction industry. Given the high influence of purchases by governments and public organizations on the European economy, it is important to direct public procurement towards “green public procurement” (GPP), which promotes sustainable practices including the reuse of materials and products, by integrating “green criteria” into public contracts.
This article will delve into the main challenges associated with the reuse of wood products left after demolition and cover possible solutions that can facilitate such reuse. Acknowledging the significant role that public procurement plays in the construction sector, we will identify challenges that should be addressed in the “reuse of wood products left after demolition” under GPP framework and explore potential solutions.
Green Public Procurement (GPP)
GPP encourages sustainable purchasing practices with reduced environmental impact through selection of environmentally friendly criteria for public contracts.
Since 2008, the Commission has developed over 20 GPP criteria applicable in the EU, which are continuously updated and reviewed (European Commission, 2016). Apart from EU’s level GPP criteria, national or regional criteria may exist for various products and services, for example, in Finland, under Finnish Act 1397/2016 “On Public Procurement and Concession Contracts”, public authorities are required to promote sustainable procurement practices by including the use of eco-labels and sustainable criteria in tender specifications.
Helsinki on its way to “greener” construction practices
Helsinki’s Circular Economy Cluster Program participates in multiple projects focusing on resource efficiency, waste reduction, and overall GHG (GreenHouse Gas) reduction. Among the projects are the ones that aim to reuse construction products left after demolition. A share of such products includes wood products, which might be reused especially within green public procurement, which is an effective mechanism to promote such sustainable practices. To access the reuse of building materials in construction projects a special tool was created for the Helsinki Circular Economy Cluster program which compiles product eligibility specifications as part of site-specific verification (Helsinki Circular Economy Cluster, 2023).
Helsinki’s challenges in the reuse of wood products left after demolition
Reuse of wood products left after demolition is not a ubiquitous practice, and Helsinki City had to address multiple challenges while running construction projects:
- Monitoring and supervision challenges: Supervision practices are constrained due to a lack of digital tools, clear criteria, and guidelines for all participants, including those involved in sorting practices on the demolishing sites. Such limitations prevent accountability and organizational oversight.
- Lack of experience: The reuse of wood products left after demolition is in the development stage and mostly executed via pilot projects which is not sufficient for the industrial scale. The limited expertise of the operators in demolishing practices prevents fast progress. Moreover, it is time-consuming, mainly performed manually due to lack of technologies, can be dangerous and after all, the removed parts will mostly not be used for the same purpose because they might require refurbishment or be in poor condition, thus not meeting high energy and safety standards. In general, wood products left after demolition have limited possibilities to be recycled and even fewer chances to be reused. Since the reuse of wood products is not a one-action process, sometimes it can lead to an increase in carbon footprint associated with additional operations such as transportation, the need for refurbishment, additional energy consumption to support the activities, or burning it if treated as waste.
- Legal ambiguity and lack of harmonized assessment methods: Lack of harmonized European rules, and the absence of Finnish assessment methods for construction works restrain the potential for the reuse of wood products left after demolition. Leaving the issue to be regulated at the national level results in the differentiation of requirements between European countries and variations in the assessment of reused components in new construction. Unlike criteria for CO2 assessment, EN standards applicable to reused construction products do not yet exist which results in uncertainty of assessment methods and different application of EU Construction Product Regulation. In scenarios where wood products left after demolition are considered waste, it is almost impossible to get end-of-waste status for their legal reuse in a new construction
- High costs: At the moment, the reuse of wood products left after demolition seems to be financially unsustainable and mostly performed on a case-by-case basis through pilot projects. Bringing reuse initiatives on an industrial scale is challenging due to unclear requirements for the reuse of wood products in Construction Product Regulation, scarcity of real demand, high costs linked to the reuse of wood products left after demolition, along with absence of financial incentives for the participants and willingness of operators to invest money in processes. One of the reasons for high costs is that most buildings are not designed in a way to be deconstructed, thus, the reuse of wood products cannot be paid enough to cover the costs of disassembly and it is cheaper to buy new materials than to utilize reused ones. Additionally, demolishing, refurbishing, storage, and transportation also incur extra fees.
- Absence of functional reuse market: Development and successful implementation in business models of reused wood products left after demolition require a functional demand-supply mechanism. Currently, the reuse market is in a state of stagnation without any dynamic development. Development of the reuse market requires integration of more operators into the process, more open-source APIs, new technology like standardized “data space” and multiple functional digital marketplaces like “kiertoon.fi”, where API integration links the demolition survey application with the digital market space for data exchange. Despite Helsinki’s strategy to increase the share of reused wood products in the construction sector the volume of such products is still relatively low and it is challenging to find new construction sites where such reused wood products could be utilized.
Helsinki’s approach to facilitate the reuse of wood products left from the demolition
The reuse of wood products brings direct and indirect environmental benefits which can be traced through reduced consumption of raw materials, reviving of biodiversity, and overall carbon footprint reduction. Helsinki’s approach to facilitate the reuse of wood products left after demolition based on the results of the projects includes the following recommendations:
- Monitoring and supervision support: It is recommended to have a thorough pre-survey and report obligations to sales platforms regarding wood products left after demolition. Demolition-survey applications could assist in the creation of a list of products produced after demolition which include characteristics of the wood products intended for reuse. Thorough sorting of the products for further reuse already on the construction site can reduce the efforts required for testing them as part of the designation of validity and can help their cataloguing to show them to potential buyers.
- Increase of expertise and knowledge: technical support via digital sales platforms like “Materiaalitori” or “Purkukartoitussovellus” can increase the flow of reused wood products left after demolition, by providing information directly to construction planners, architects, and other parties starting from the earliest stages of the design process. The facilitation of reuse is directly connected with a need for learning and benchmarking, which can be achieved through analysis of the results of successful projects run in Finland and other countries. For example, in Finland, demolition practices from construction projects include the reuse of timber frame structures left after demolition in new construction projects or the reuse of salvaged planks for design furniture.
- Overcoming legal ambiguity: Until the EU-standard methods for assessing the reuse of wood products left after demolition are developed, in Finland, on a local level it is possible to utilize own tools which help participants to use the same method for designation of validity. For example, the Helsinki Circular Economy Cluster offers an Excel file with the assessment criteria for the reuse of wood products (Helsinki Circular Economy Cluster, 2023). Moreover, in some cases, it is possible to utilize existing old plans of the building where quality characteristics of the product are provided. Also, the results of the demolition and usability surveys can be utilized. For certain categories of wood products, a demonstration of eligibility can be provided on a construction site basis, including a visual examination. Additionally, wood products can be reused in a lower requirement class than their original purpose, for example, bearing logs reused for non-bearing structures.
- Cost reduction and incentives: Significant savings for the operators regarding the reuse of wood products left after demolition can be achieved through developments in logistics and available storage places within the same location for construction products intended for further reuse. The New Construction Act, EU-taxonomy, and latest requirements for low-carbon buildings promise to provide feasible incentives that in return could reduce the costs of reusable products making them more affordable for buyers compared with a new product. To make reusable wood products more affordable, prices for raw materials have to become higher in the future along with the increase in emissions trading prices.
- Development of the reuse market: Public authorities can support that the operational environment is more predictable to stimulate investments in efficient and cost-effective processes of reused construction products. It has to become economically profitable to reuse wood products rather than recycle, burn, or purchase new ones.
Helsinki’s GPP experience with criteria ”Reuse of Wood Products Left after Demolition”
The reuse of wood products left after demolition as green criteria has not been integrated into full-scale projects run by Helsinki City. Nonetheless, the results of the pilot projects revealed challenges and possible solutions in GPP which can undergo further analysis to scale up the reuse initiatives.
- Choice of the approach – voluntary or mandatory GPP:
- From one side, the voluntary nature of reuse criteria in GPP contracts may not be as effective as obligatory ones, especially since only big municipalities like the City of Helsinki have specific targets for the reuse of wood products, which are mostly tested within pilot projects. In this regard, a mandatory approach to GPP could provide a clear national perspective.
- On the other side, premature mandatory rules could lead to excessively high costs, particularly due to challenges associated with qualification criteria for reuse, verification methods, operator shortages, storage-related issues, a lack of feasible business potential, and market demand.
In light of diverging perspectives, initial support can be voluntary until establishing a functional reuse market and clear guidelines, particularly regarding assessment methods, verification, and the reuse status.
2. Obstacles for implementation the “reuse” criteria
Currently, in GPP practices of Helsinki City, there is no requirement for all demolition projects to reuse wood products left after demolition since there are practical uncertainties associated with:
- Legal obscurity regarding when, how, and in what parts of the building wood products left after demolition can be reused and what needs to be verified
- A need for revision of the European norms for adaptability to reclaimed elements and the Waste Framework Directive (WFD) regarding waste status for reused construction products.
- The non-functional market and lack of demand for reused wood products, which are unaffected by whether demolition projects necessitate dismantling or not.
- High costs associated with projects with the “reuse criteria” compared to traditional ones. Thus, there is little business potential until significant changes occur in the market and more expertise is obtained.
3. What should be the focus to support the GPP practices with the “reuse” criteria?
From Helsinki City’s side, facilitation for the reuse of wood products within a GPP could be achieved by piloting the reuse of wood products in new-build projects and utilizing minimum requirements as well as quality points in demolition ones. Moreover, it is important to focus on:
- Establishment of common assessment methods. For example, a Helsinki Circular Economy Cluster program developed a common assessment method that could be utilized by operators to verify eligibility for the reuse of construction products, including wood products left after demolition, particularly windows, doors, and glulam (Helsinki Circular Economy Cluster, 2023).
- Compulsory pre-demolition audit to prevent reused wood products left after demolition from being unnecessarily classified as waste
- Establishment of a common sales platform with an open collaboration between all participants involved in the process, enabling the possibility to share best practices, develop expertise, and benchmark
- The company’s strategy should support GPP practices across all stages of the project, including the planning of demolition, receiving permits, and handling product suitability
- Upcoming changes in legislation (CPR, WFD, and EU taxonomy) could facilitate the reuse of wood products left after demolition, thereby encouraging contractors to implement new cost-effective operational methods
4. How to facilitate provisions in public contracts with the “reuse” criteria
The “reuse” criteria in GPP contracts must provide clear characteristics of products before the bidding process to help suppliers understand what is demanded. Moreover, the contract provisions should:
- Clearly indicate what will be reused, where the reused materials will be stored, who pays for dismantling and refurbishment, and, in case of resale, potential buyers for used products
- Be explicit, however, clear characteristics should not exclude the possibility for suppliers to suggest alternatives.
- Be based on market analysis and suppliers’ capabilities, meaning that the demolition company should have the possibility to calculate the number of materials, they can resell beforehand.
5. “Minimum requirements” or “quality points” in the contract?
The choice varies depending on the contracting party involved. While suppliers might prefer minimum requirements due to uncertainty in scoring quality points, procurers might focus on minimum requirements due to unwillingness to compromise on certain aspects.
Regardless of the choice, both requirements need lots of effort from the City. Given that neither requirement has been regularly utilized so far, the general recommendations drawn from the results of pilot projects and stakeholders’ opinions can include the following:
- Clear minimum requirements should be set in the GPP contract before contracting a demolition
- For quality points to be attractive they should be sufficiently clear, and be financially viable, where the added value compensate for the increase in costs, however, ensuring that procurement is not solely based on price.
- As an illustration, the minimum requirement in the contract suggested by Helsinki’s City side can be “imposing a ban on burning demolition wood for energy purposes”; the minimum requirement suggested from a supplier’s side can be “reporting and clarification” obligations on the reuse. An example of a quality point from the procurers can be ”having reused materials in certain parts of the building”; whereas suppliers suggested receiving quality points in case of “exceeding the minimum requirements”.
CONCLUSIONS:
EU and national policies promoting the idea of reuse are not sufficient without the establishment of a functional reuse market, as well as financial and economic incentives encouraging operators to prioritize reuse over the consumption of raw materials.
- Expected changes in legislation, including the Waste Framework Directive (WFD), the Construction Products Regulation (CPR), and EU Taxonomy could boost the reuse of wood products left after demolition, through the development of harmonized standards for assessment, mandatory pre-demolition audits, reporting requirements for the reuse, and incentive measures.
- The engagement of private recycling operators, offering services in disassembly, refurbishment, storage of building components, and the capability to verify eligibility, are essential for reusing wood products left after demolition.
- The voluntary mechanism of GPP with green criteria can be a good start within pilot projects, however, it is not powerful enough to change entire construction practices on a larger industrial scale; regulatory changes are required.
Resources:
European Commission. (n.d.). EU taxonomy for sustainable activities. Finance. https://finance.ec.europa.eu/sustainable-finance/tools-and-standards/eu-taxonomy-sustainable-activities_en
European Commission. (2016). Buying green: A handbook on green public procurement,3rd Edition. https://sustainable-procurement.org/fileadmin/user_upload/layout/Documents/Buying-Green-Handbook-3rd-Edition.pdf
Helsinki Circular Economy Cluster. (2023). It is now easier to reuse construction products that have been removed intact – check out the definitions for demonstrating product suitability. Testbed Helsinki. https://testbed.hel.fi/kiertotalous/kirjasto/ehjana-irrotettujen-rakennustuotteiden-uudelleenkaytto-on-nyt-helpompaa/