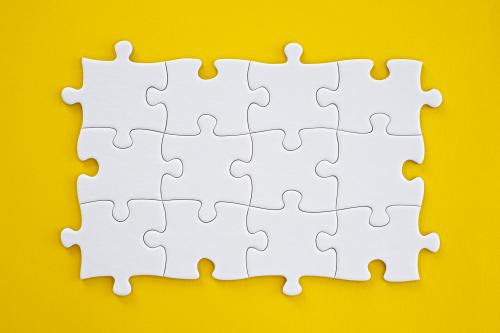
Miten 5S-menetelmän avulla voidaan parantaa yrityksen kannattavuutta?
Kannattavuus on keskeinen tekijä yrityksen toiminnan jatkuvuuden kannalta. Yrityksen näkökulmasta kannattavuutta parantavat tehokkuus ja tuottavuus, jotka ovat toinen toistaan tukevia tavoitteita. Miten yritys pääsee mahdollisimman tehokkaaseen ja tuottavaan tuotantoprosessiin?
Tasapainottelua tehokkuuden muotojen välillä
Tänä päivänä useat yritykset tähtäävät edelleen resurssitehokkuuteen. Resurssitehokkaassa toiminnassa yrityksen resurssit tuottavat yritykselle mahdollisimman paljon arvoa, koska niiden toiminta on jatkuvaa. Nopeasti ajateltuna resurssitehokkuus voikin kuulostaa yrityksen kannalta hyvältä ratkaisulta. Modigin ja Åhlströmin mukaan lopulta syntyy tehokkuusparadoksi, kun yritys keskittyy liikaa maksimaaliseen resurssien käyttöön (Modig & Åhlström 2013, 100–126). Tehokkuusparadoksi aiheuttaa lisätöitä, joita ei olisi päässyt syntymään, mikäli yritys olisi alusta asti keskittynyt asiakkaan ensisijaisen tarpeen ratkaisemiseen.
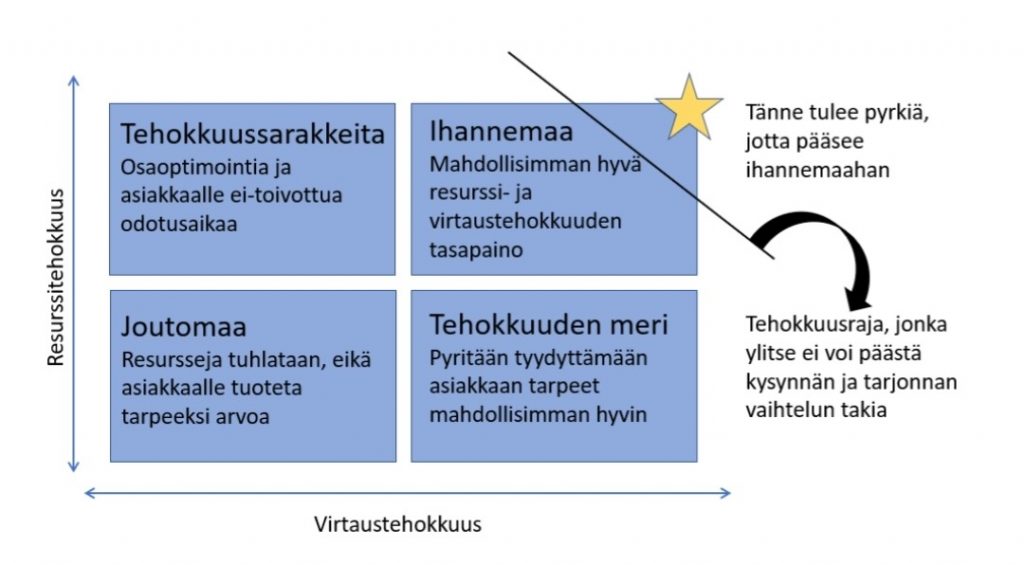
Resurssitehokkuuden vastapari on virtaustehokkuus, joka on Lean-filosofiassa tehokkuuden vallitseva muoto. Resurssitehokkuutta ei kuitenkaan sovi unohtaa kokonaan, vaan pyrkimys hyvään virtaus- ja resurssitehokkuuden tasapainoon on keskiössä. Virtaustehokkuudella tarkoitetaan, että yrityksen tuottamaa arvoa tarkastellaan asiakkaan näkökulmasta. Ne toiminnot, jotka lisäävät arvoa asiakkaalle ovat merkityksellisiä ja niihin yrityksen tulee keskittyä. Ylimääräisiä, arvoa lisäämättömiä vaiheita, kutsutaan hukaksi. Hukkaa ovat esimerkiksi tehokkuusparadoksin seurauksena syntyvät lisätyöt ja liian suuret varastotilat. Jotta yritys voi korostaa virtaustehokkuutta, sen täytyy päästä ylimääräisestä hukasta eroon. Yksi Lean-filosofian työkalu, joka keskittyy hukan poistoon, on 5S-menetelmä.
Viisi ässää ja niiden hyödyt
5S-menetelmä on viisivaiheinen työympäristön organisointimenetelmä, jonka avulla parannetaan työympäristön toimivuutta. 5S-menetelmän vaiheiden nimet tulevat Japanin kielestä ja ne ovat:
- Seiri – Lajittele
- Seiton – Järjestä
- Seiso – Puhdista ja huolla
- Seiketsu – Vakiointi
- Shitsuke – Seuranta
Vaiheet toteutetaan säännöllisesti, jolloin huolehditaan tilan jatkuvasta kehityksestä ja 5S-menetelmän ylläpidosta. Lajitteluvaiheessa kaikki tilassa ja työpisteillä olevat välineet käydään läpi ja ylimääräisistä välineistä hankkiudutaan eroon. Tämän vaiheen avulla vältytään ylimääräisiltä varastointitiloilta ja säilytystiloilta. Kun välineet on käyty läpi, jäljelle jääneet välineet järjestetään omille, merkityille paikoilleen. Järjestä-vaihe auttaa pitämään tarvikkeet paikoillaan, jolloin aikaa ei kulu niiden etsimiseen. Kolmannessa vaiheessa tilat ja välineet puhdistetaan ja huolletaan. Tämän avulla saadaan pidettyä yllä siistiä ulkoasua työtiloissa sekä varmistettua välineiden toimivuus ja pidennettyä niiden käyttöikää. Kaksi viimeistä vaihetta liittyvät menetelmän vakiointiin ja seurantaan. Vakioinnin avulla työtavat saadaan osaksi jokapäiväistä työskentelyä, jolloin 5S-menetelmää on helppo ylläpitää. Seuranta-vaiheella seurataan menetelmän toteutumista ja saadaan näin tietoa työympäristön tilasta.
Millaisia vaikutuksia 5S-menetelmällä voidaan saavuttaa?
Eri vaiheiden hyötyjen lisäksi 5S-menetelmän käyttöönotto luo toimivia työskentelytapoja ja parantaa työympäristöä. Siisti ja järjestyksessä oleva työympäristö tuo ammattimaisemman kuvan yrityksestä. 5S-menetelmä tuo myös Lean-filosofian konkreettisesti näkyväksi työpaikalle. 5S-menetelmän hyötyjä voidaan tarkastella yrityksen, asiakkaan ja henkilöstön näkökulmasta. Käydään näitä hyötyjä läpi seuraavaksi.
Yrityksen näkökulmasta 5S-menetelmän hyödyntäminen lisää kannattavuutta, kilpailukykyä, henkilöstön viihtyvyyttä ja parantaa toimitusvarmuutta sekä laatua. Positiiviset vaikutukset vahvistavat toinen toisiaan. Kannattavuuden paranemisen taustalla voi olla esimerkiksi kustannusten laskua, kun tuotannon läpimenoajat ovat lyhentyneet ja ylimääräisistä varastointitiloista on voitu luopua hyvän järjestelyn ja lajittelun ansioista. Laadun ja yleisen siisteyden paraneminen lisäävät arvoa asiakkaan näkökulmasta. Kun hukan poistamisen jälkeen asiakkaan tarve pidetään tuotannon aikana keskiössä, tuotteiden läpimenoaika lyhenee ja toimitusvarmuus paranee. On tutkittu, että 5S-menetelmää ja Lean-filosofiaa hyödyntävät yritykset ovat kilpailukykyisempiä. Kilpailukyvyn paranemiseen johtaa jatkuvan parantamisen periaate.
Henkilöstön viihtyvyys on yritykselle tärkeää, mutta erityisen tärkeää työn viihtyvyys on henkilöstön näkökulmasta. 5S-menetelmän avulla pystytään parantamaan työturvallisuutta, jonka ansioista läheltä piti -tapahtumat ja työtapaturmat vähenevät. Siistissä ja järjestyksessä olevassa työympäristössä on turvallisempaa ja mielekkäämpää työskennellä, kuin työympäristössä, jossa työaikaa kuluisi jatkuvasti toissijaisiin asioihin. Havaintoja on helpompi tehdä, kun työtä normaalisti tekevät henkilöt saavat itse seurata 5S-menetelmän toteutumista ja kehittää sitä. Henkilöstön mukaan ottaminen työympäristön ja työtapojen kehittämiseen lisää ymmärrystä siitä, miksi näin toimitaan. Yksilön hyvinvoinnin lisäksi henkilöstön viihtyvyydellä on positiivisia vaikutuksia yrityksen toimintaan. Motivoitunut henkilöstö työskentelee tehokkaammin ja huolellisemmin.
Miten 5S-menetelmän käyttöönotto näkyy Finnsementin betonilaboratoriossa?
Opinnäytetyön aiheena oli 5S-menetelmän käyttöönotto Finnsementin betonilaboratoriossa. Lähtötilanteessa betonilaboratorion haasteita oli esimerkiksi vähäinen varastotila, työajan kuluminen toissijaisiin asioihin sekä puutteellinen työergonomia. Opinnäytetyön tavoitteena oli parantaa työturvallisuutta, työympäristön ulkoasua ja toimivuutta. Näihin haasteisiin lähdettiin vastaamaan 5S-menetelmän käyttöönotolla.
Pidemmän aikavälin vaikutuksia on näin varhaisessa vaiheessa hankala arvioida, mutta lyhyemmän aikavälin tavoitteisiin päästiin 5S-menetelmän avulla. Työtila saatiin järjestettyä siten, että ylimääräinen kulkeminen eri työpisteiden välillä väheni. Kaikille tavaroille, näytteille ja välineille saatiin määritettyä omat paikkansa, jolloin päästiin eroon niiden etsimisestä. Työtilan siisteys parani ja sitä on helpompi ylläpitää. Ylimääräisistä tarvikkeista ja näytteistä päästiin eroon, minkä ansiosta saatiin lisää säilytystilaa. Työn ergonomia parani tekemällä korkeusmuutoksia työpisteillä. Ergonomian toteutuminen huomioitiin myös työturvallisuusohjeissa. Paremmin toimiva työympäristö on vaikuttanut positiivisesti työntekijöiden kokemaan työn mielekkyyteen sekä työajan kulumiseen olennaisiin asioihin.
5S-menetelmän ylläpidon kannalta työtapojen vakiintuminen vie varmasti oman aikansa. Vakiinnuttamisen tueksi tehtiin 5S-työohje. 5S-menetelmän kehitysideoita kerätään seurantaa varten tehdyllä lomakkeella. Tulevaisuudessa pääsemme toivottavasti kehittämään 5S-menetelmää lisää ja laajentamaan sen käyttöä koko betonilaboratorion toimintaan ja näytelogistiikkaan.
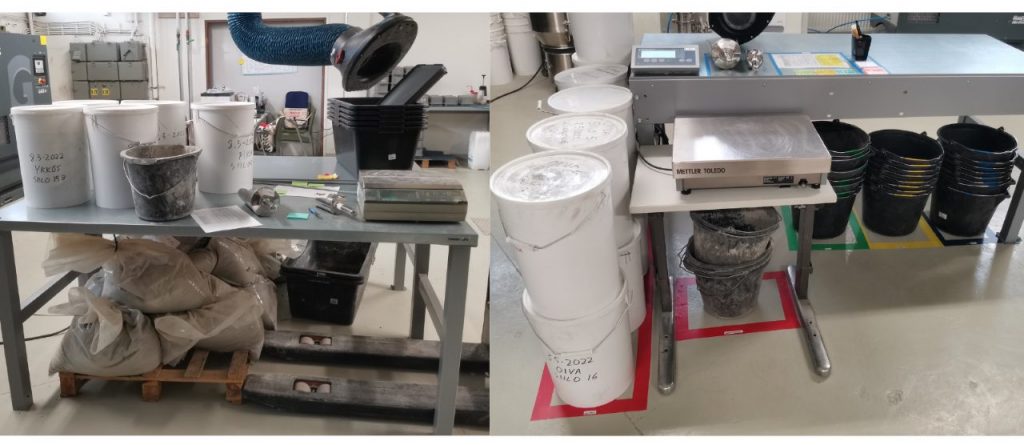
Opinnäytetyö: 5S-menetelmän ja työturvallisuuden edistäminen betonilaboratoriossa.
https://urn.fi/URN:NBN:fi:amk-2022060816485
Lähteet
Niklas Modig, Pär Åhlström. 2013. Tätä on LEAN. Tukholma : Rheologica publishing, 2013.
Kouri, Ilkka. 2009. LEAN taskukirja. Helsinki : Teknologiateollisuus ry, 2009.
Tuominen, Kari. 2010. Lean, Tehoa ja laatua siisteyden ja järjestyksen kehittämiseen—5S. Helsinki : Readme.fi, 2010.