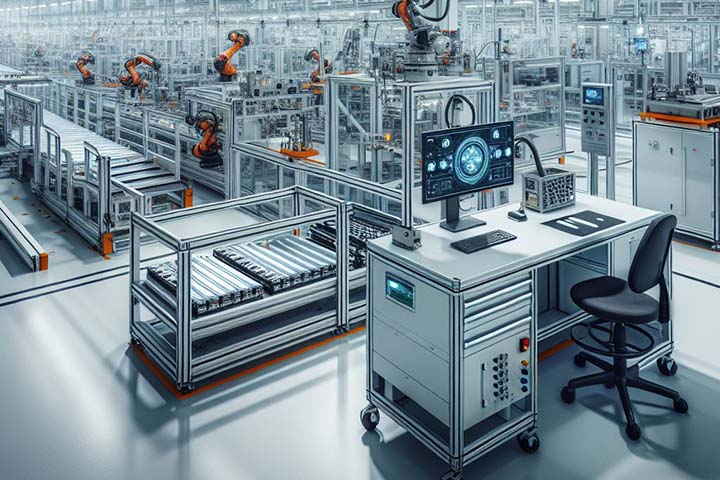
Fiksumpaa palautusta robottisolulla – kuinka parantaa tuottavuutta ilman turhia investointeja?
Valmet Automotive EV Powerin tuotantolinjalla toteutettu opinnäytetyö keskittyi harvoin käytössä olevan viallisten tuotteiden käsittelypisteen, eli NOK-aseman hyödyntämiseen tehokkaammin. Työssä arvioitiin, miten tätä robottisoluun kuuluvaa asemaa voitaisiin käyttää paitsi epäkelpojen, myös hyväksyttyjen tuotteiden palautukseen. Tavoitteena oli parantaa tuotannon sujuvuutta ja vähentää manuaalista työtä pienin, mutta vaikuttavin muutoksin.
NOK-asema alikäytössä – ongelma vai mahdollisuus?
Opinnäytetyön alkuvaiheessa tehty seuranta osoitti, että NOK-asema oli käytössä keskimäärin vain 0,33 kertaa päivässä, mikä tarkoittaa noin yhtä käyttökertaa kolmessa päivässä. Tämä herätti kysymyksen investoinnin järkevyydestä, sillä vähäinen käyttö ei perustellut laajaa automaatiokehitystä. Analyysin pohjalta kävi kuitenkin ilmi, että NOK-aseman alikäyttö itsessään tarjosi myös mahdollisuuden: resurssi oli teknisesti toimiva ja riittävästi varusteltu, mutta käyttötarkoitus oli liian suppea. Sen sijaan, että asemaa pidettäisiin vain NOK-tuotteita varten, ryhdyttiin selvittämään, voitaisiinko sitä hyödyntää osana tuotantoprosessin normaalia kulkua.
Laatupiste molempiin suuntiin
Ratkaisuksi ehdotettiin, että NOK-asemasta tehtäisiin myös OK-tuotteiden palautuspiste, eli ns. quality inlet/outlet. Näin sama robottisolu voisi käsitellä tuotteita molempiin suuntiin, ja manuaalinen kuljetustyö työpisteen ja linjan välillä vähenisi. Seuranta-aikana palautuksia tehtiin keskimäärin kolme kappaletta päivässä, ja niihin kului yhteensä jopa 411 minuuttia kuukaudessa.
Uuden toimintamallin ansiosta palautukset eivät enää sitoisi työntekijöitä pitkiksi ajoiksi kuljetustehtäviin tai odottamaan vapautuvaa paikkaa linjalla. Lisäksi tämä vähentäisi kyseisen työpisteen ruuhkautumista tilanteissa, joissa useita tuotteita olisi odottamassa palautusta. Ratkaisu tehostaisi tuotannon kokonaisprosessia ja toisi lisää joustavuutta resurssien käyttöön. Samalla vapautuisi henkilöstön aikaa muihin tuottavampiin tehtäviin, mikä tukee Lean-filosofian periaatteita ja jatkuvan parantamisen ideologiaa.
Lean ja robotiikka yhdessä
Opinnäytetyössä sovellettiin Lean-ajattelua tunnistamalla ja poistamalla tuotantoprosessista turhia, lisäarvoa tuottamattomia vaiheita. Tässä tapauksessa havaittiin, että tuotteiden manuaalinen kuljettaminen NOK-asemalta takaisin tuotantolinjalle oli merkittävä hukka. Lean-ajattelun ytimessä on asiakkaalle lisäarvoa tuottavien toimintojen maksimoiminen ja kaiken muun, eli hukan, poistaminen. Tällaisia hukkaa aiheuttavia toimia voivat olla esimerkiksi turhat kuljetukset, odotukset ja manuaaliset siirrot.
Tässä tapauksessa suurimmat tuotannolliset hukan lähteet liittyivät palautettavien tuotteiden manuaaliseen kuljettamiseen työpisteeltä takaisin tuotantolinjaan. Tämä ei ainoastaan kuluttanut aikaa vaan myös kuormitti työntekijöitä ja aiheutti katkoja muuhun työskentelyyn.
Suurten laiteinvestointien sijaan keskityttiin olemassa olevien resurssien parempaan hyödyntämiseen. Ratkaisuksi ehdotettiin robottiohjelman päivitystä sekä viivakoodinlukijan lisäämistä varmistamaan, että vain oikeat tuotteet palaavat linjalle. Tämä lähestymistapa tukee Lean-filosofiaa konkreettisesti: tehdään enemmän vähemmällä, turvallisesti ja laadukkaasti.
Säästöjä pienellä investoinnilla
Arvioitu investointi robottisolun ohjelmointiin ja kahteen viivakoodinlukijaan oli noin 2000 euroa. Laskelmien mukaan takaisinmaksuaika olisi noin kaksi vuotta, mikä tuotannollisessa mittakaavassa on kohtuullinen. Säästöjä syntyy erityisesti siitä, kun työntekijöiden aikaa ei enää kulu tuotteiden palautuksiin samalla tavalla kuin aiemmin, ja lisäksi palautusprosessi nopeutuu. Jatkossa näitä vapautuneita resursseja voidaan ohjata esimerkiksi laadunvalvontaan tai muuhun arvoa tuottavaan työhön.
Pohdintaa ja jatkoideoita
Työ osoitti, että automaation lisääminen ei aina vaadi merkittäviä investointeja uusiin koneisiin tai teknologioihin. Pienilläkin muutoksilla voidaan saavuttaa merkittäviä parannuksia, kunhan prosessia tarkastellaan kriittisesti ja ymmärretään sen pullonkaulat. Kehitysprojektin aikana korostui tarve jatkuvalle seurannalle ja tiedolla johtamiselle: seuranta-aineiston avulla voitiin osoittaa, missä ongelmakohdat todella sijaitsivat. Jatkokehitysideana ideoitiin jigin lisäys NOK-pöydälle, jonka avulla palautettavat tuotteet saataisiin palautettua robotin käsittelyyn aina optimaalisessa asennossa.
Lähde
Lahti, E. 2024. Not OK -aseman automatisointitason nostaminen – Theseus, Turun ammattikorkeakoulun opinnäytetyö.