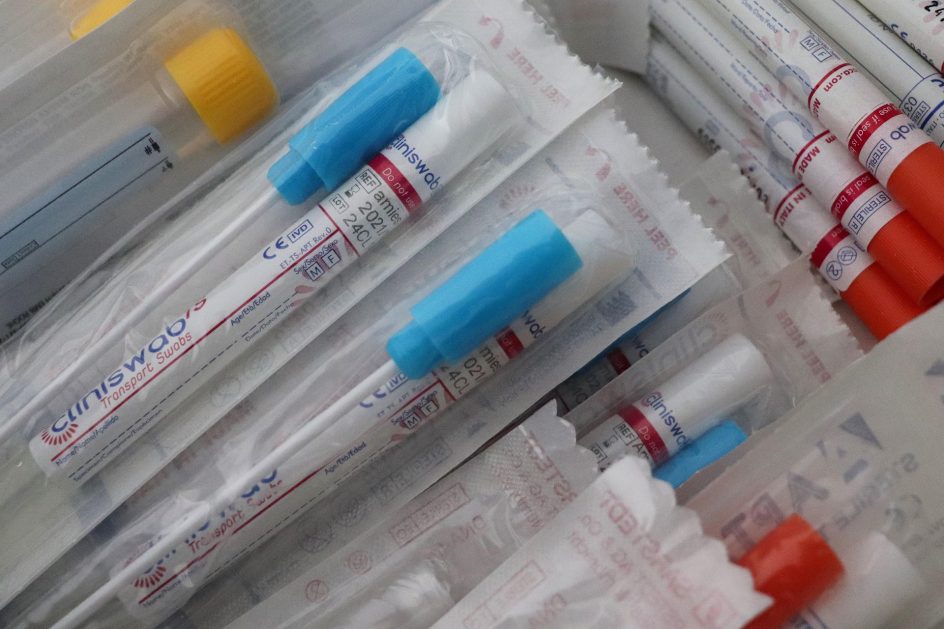
Continuous monitoring of product quality metrics in medical device field
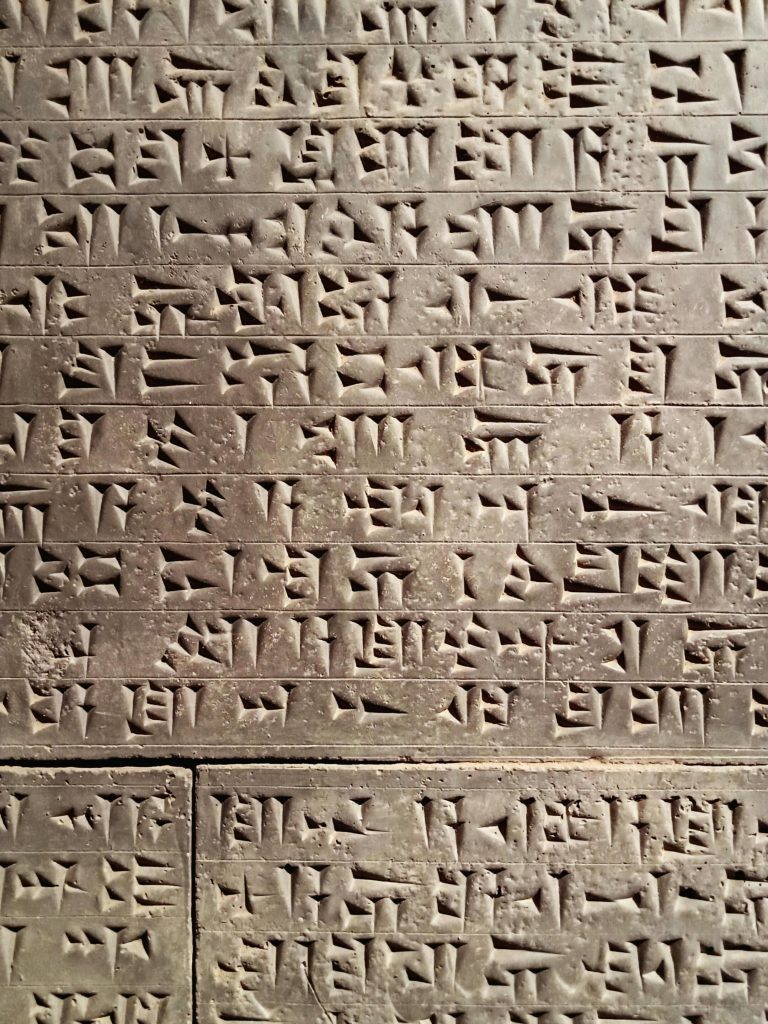
From clay tablets to automatic PowerBI dashboards. One of the oldest pieces of documentation, is a clay tablet, that describes customers dissatisfaction towards bought copper. Let´s say that this piece of clay tablet filled with statement written in cuneiform, is a starting point of the long history of recorded customer complaints.
Introduction
Medical device and in vitro diagnostic devices form a field, that is highly regulated. Manufacturers and developers in the field have to aim to continuous improvement with their products and services. Due to the nature of the products and services, user and patient safety and satisfaction are in the heart of this improvement process. For manufacturers and developers to know what to improve and what to prioritize, they are required by regulations (EU MDR & IVDR, FDA 21 CFR Part 820) to continuously monitor product quality related metrics. These metrics include quality issues like customer complaints, non-conformances and Corrective action and Preventive actions (CA/PAs). By defining well and in detail what is expected from product and/or service and what are critical for the intended use, manufacturers and developers can plan and act on these improvement needs. By setting thresholds for the amount of new customer complaints, non-conformance trends or CA/PA through-put times, manufacturer can not just evaluate their product quality but also the efficiency of the quality management system and amount of resources. In addition to regulatory bodies, internal stakeholders require also periodic reporting of these key metrics. In many cases complicated problems become solvable with cross-functional collaboration and this require sharing the information and making available and up to date.
Development
The scope of the project was limited to a biotechnology company manufacturing IVD products. The starting point for the thesis was the current monitoring process of product quality metrics, which consisted of customer complaints, non-conformances and CA/PAs. There were defined metrics, thresholds and well-documented records of each of these quality issues. What was missing, was a continuous monitoring and automated analysis of the key quality issue metrics. The thesis aimed to create a PowerBI dashboard of selected product quality and QMS efficiency metrics, that would provide an up-to-date view of each product line and product. By automatizing the monitoring process, the needed data analysis is always within the reach of quality, regulatory and product specialists. Now this data processing relies heavily on manual work and the tactile knowledge of product specialists. Service design framework (double diamond) was utilized in the planning of new process of continuous monitoring. Based on the interviews and observations of various teams and professionals and user requirements, it was clear that the current process needed an aligned process and automated platform and process to enable more collaboration between stakeholders.
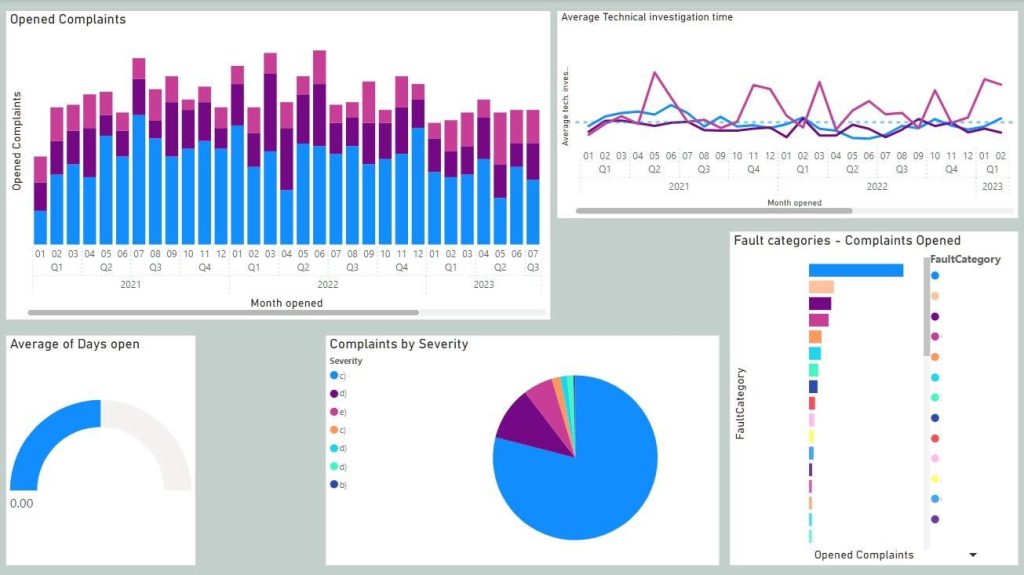
Product quality metrics
- Quality issue counts per month/Quarter/Year
- Through-put time of quality issue
- Fault categories/Root cause trends
- Risk severity trends
Results
PowerBI dashboard provided a modifiable overview of selected product quality and QMS efficiency metrics, by processing the raw data of quality issues with their metadata. The overview is refreshed automatically once a day, or by request, and it includes data of three different product lines and hundreds of products. To ensure that dashboards are usable for a wide audience and serve the different reporting needs, each dashboard is filterable at a minimum by product, product line, opening and closing time, fault category and risk severity.
The automatic analysis of quality issue data and fulfilled user requirements for continuous monitoring process ensure the compliance with regulatory and internal reporting responsibilities and enables the company to aim towards continuous improvement of products and services.
Sources:
Thesis: Fanny Wiik-Miettinen. 20224. Continuous monitoring of metrics in medical device field https://urn.fi/URN:NBN:fi:amk-2024111328042
Figure 1: Pexels, Ersan Yilmaz
Figure 2: Thesis, Fanny Wiik-Miettinen