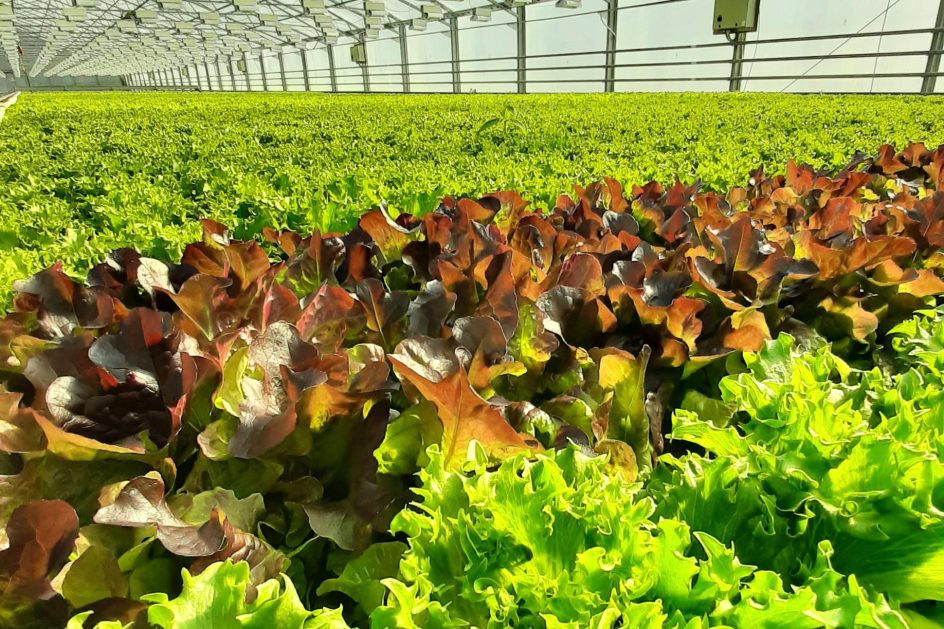
Miten tehostimme kasvihuonetuotannon prosesseja Lean menetelmillä?
Tämä artikkeli perustuu pääkirjoittajan opinnäytetyöhön, jonka tarkoituksena oli tuotannon kehitys kasvihuonetuotannossa sadonkorjuun ja lähettämön välillä. Siellä suurimmaksi kehityskohteeksi oli todettu työpäivän aikana liian nopeasti muuttuvien asiakastilauksien aiheuttama vaihtelu tuotannon jokapäiväisessä toteutuksessa.
Kehittämistehtävän lähtökohdat
Opinnäytetyössä lähdettiin liikkeelle nykytilan kartoituksesta, jossa piirrettiin nykyisestä tuotantoprosessista tarkka vuokaavio sekä arvovirtakuvaus. Myös samaan aikaan aloitettiin tuotannon parantaminen ja prosesseihin liittyvän kirjallisuuden lukeminen. Tietoa ja kirjallisuutta löytyy todella laajasti tuotannon kehittämisen osalta ja monet niistä liittyvät Toyota Production Systemsiin (TPS) pohjautuvaan Lean-ajatteluun. Opinnäytetyön tekijän lukiessa aihepiirin kirjoja, tuli selväksi, että Lean on käsitteenä todella laaja ja sitä voidaan hyödyntää paljon muuallakin kuin pelkästään tuotantoympäristössä. Selväksi tuli myös se, että mitään valmista mallia ei ole tarjolla, vaan jokaisen on itse perehdyttävä riittävällä tasolla Lean-ajatteluun ja räätälöidä tarpeen mukaan parantavat toimenpiteen kehityskohteeseensa. Kirjallisuutta pidemmälle lukiessa opinnäytetyön tekijä perehtyi virtaustehokkuuteen, ja sen parantamisen hyödyllisyyteen.
Virtaustehokkuutta parantamalla vaikutetaan positiivisesti myös resurssitehokkuuteen, jos myös vaihtelua saadaan pienennettyä. Opinnäytetyön nimeksi muodostui: ”Developing production flow effiency -From harvest to dispatch”. Mike Rotherin kirja Toyota Kata avasi silmiä ja tarjosi uusia näkökulmia Lean-parantamiseen. Kaikkea ei kannata ryhtyä parantamaan orjallisesti listojen mukaan, vaan mieluiten yhtä asiaa kerrallaan kokeillen ja testaillen esimerkiksi Plan-Do-Check-Act mallia käyttäen. Kun muutat yhtä prosessia, sillä saattaa olla vaikutusta kaikkiin muihinkin prosessin tekijöihin.
Mitä kehitystössä todella tapahtui
Nykytilan kartoitusvaiheen jälkeen alettiin pohtimaan tutkimusmenetelmiä ja yhtenä menetelmänä kehitystyöhön valittiin vertailuanalyysi eli ”benchmarking”, jossa verrataan omaa prosessia jonkin toisen yrityksen tai oman yrityksen johonkin toiseen prosessiin. Siinä vertailussa selvisi, että ei kannata tehdä asioita liian monimutkaisesti, vaan yksinkertaisuus tuo virtaustehokkuutta prosesseihin. Sekä arvovirtakuvauksista ja prosessikuvauksista selvitettiin pahimmat arvoa tuottamattoman ajan tekijät.
Arvovirtakuvauksen analysoinnissa selvisi puristussilmukka ja suunnannäyttäjäsilmukka ja ne ympyröitiin prosessin kaavioon. Toyota Katan oppien mukaan keskittyminen ensin suunnannäyttäjäsilmukan kehitykseen on kannattavinta, sillä yleensä se ohjaa myös puristussilmukan toimintaa. Opinnäytetyön tekijä päätti pitää 10 hengen ryhmän kanssa aivoriihen, jonka pohjalta hän teki samojen työntekijöiden kanssaan Cause & Effect matriisin. Tässä matriisissa oli tarkoitus tuoda esiin henkilökunnan mielestä kaikkein eniten haasteita aiheuttavat asiat prosessissa käyttäen apuna pareto-sääntöä eli 80 % seurauksista johtuu 20 %:sta syistä. Näiden kaikkien analyysien pohjalta opinnäytetyön tekijä piirsi ihanteellisen prosessin, miten prosessi tulisi toimia eli asetti prosessille tavoitetilan.
Tavoitetilan saavuttamiseksi pyrimme löytämään teknisiä ratkaisuja esimerkiksi atk-ohjelmista ja Lean-työkaluista poistaaksemme arvoa tuottamattomat tehtävät prosessista. Löysimme ohjelmiston kehittäjän avustuksella jo olemassa olevasta yrityksen myyntiohjelmasta uuden ominaisuuden, jolla tarvittava informaatio saadaan kulkemaan myynnistä tuotannon keräyslistoille suoraan ohjelman kautta. Tämän avulla säästytään informaatio-katkoksilta, puheluilta ja muulta tarpeettomalta viestittelyltä, kun on standardoidut tavat toimia ilman niitä. Myös nykyisen tuotannonseurantaohjelman parempi hyödyntäminen satoennusteraporteilla todettiin hyödylliseksi työkaluksi tuotannon ja myynnin välillä.
Puskurivaraston tarve ilmeni valmiiden tuotteiden osalta suuren asiakaskysynnän vaihtelun vuoksi. Lean-ajattelun ideana on minimoida varastot, mutta todellisuudessa pieni varasto on parempi vaihtoehto, jos se auttaa koko prosessia virtaamaan tehokkaammin. Ideaksi tähän puskurivarastoon muodostui pitää vaihtelu poissa tehtaalta ”Supermarket- ajattelulla” eli valmiiden tuotteiden kanban-imuohjauksella. Yhdeksi odotusaikoja ja virtaustehokkuutta parantavaksi toimenpiteeksi valittiin ”one-piece-flow” eli yksiosainen virtaus. Kasvihuonetuotannossa yksiosainen virtaus toimii monessa paikassa hyvin, mutta resurssien ohjauksessa löytyi parantamisen varaa.
Opinnäytetyössä tarkasteltiin prosessia sadonkorjuun työpisteen näkökulmasta edeltävää ja seuraavaa vaihetta silmällä pitäen. Resursseja keskittämällä eli tekemällä nopeammin useamman työntekijän toimesta yhdeltä kasvihuoneen pöydältä lava valmiiksi, ja siirtämällä työntekijöitä seuraavaan pöytään taas samalla tavalla, on merkittävä prossia nopeuttaja ja tehostava vaikutus. Se auttaa sekä edeltävää työvaihetta tekemään työnsä ilman odottelua että lähettämöä viimeistelemään lava valmiiksi nopeammin. Virtaus pysyy tällä yksiosaisella virtauksella myös tasaisempana.
Loppupäätelmät
Lean osoittautui hyväksi kasvihuonetuotannon kehittämismenetelmäksi ja opinnäytetyön tulokset olivat käytäntöä hyvin selkeästi hyödyttäviä.