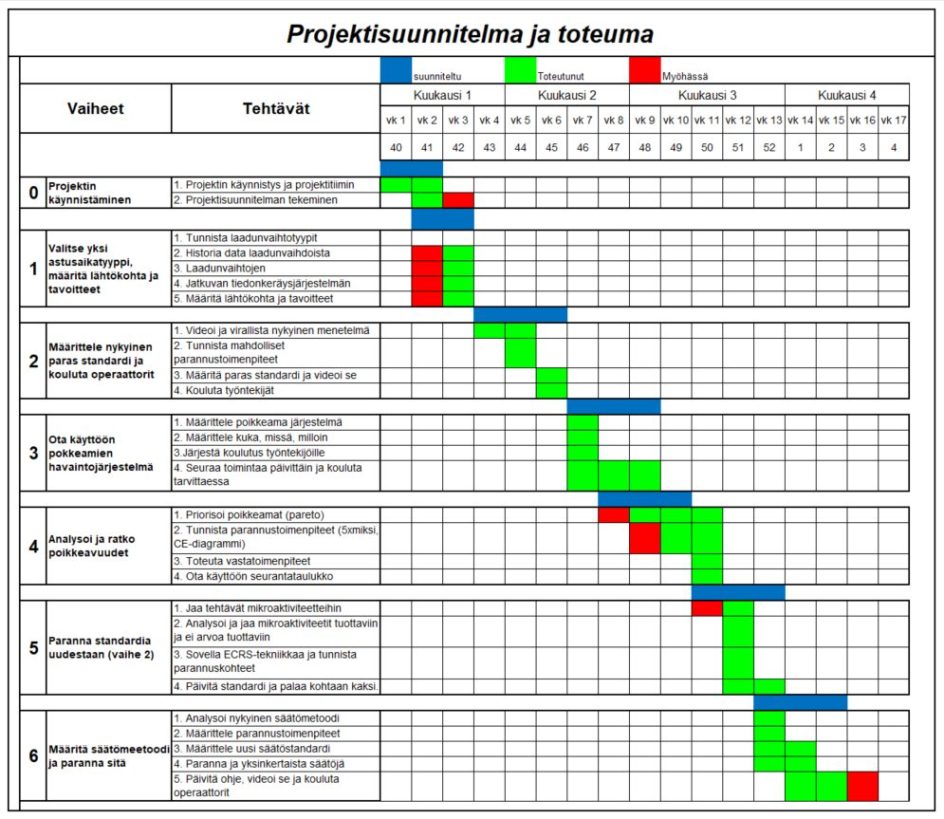
Prosessin tehokkuuden parantaminen leanin avulla –Kuinka valita oikeat työkalut hukan vähentämiseksi? Saadaanko leaniä käyttäen parannusta aikaiseksi?
Lean työkaluja käytettäessä on tärkeää ymmärtää prosessin kokonaisuus ja leanin filosofiaa syvällisemmin. Lean ei ole pelkkiä työkaluja, joita voidaan käyttää yksinään parantamisen välineenä. Kyse on kokonaisuuden ymmärtämisestä. Käyttämällä eri työkaluja käytännönläheisesti valitun metodin mukaisesti, saadaan prosessista poistettua muun muassa hukkaa. Jotta tämä kaikki olisi mahdollista ja tulokset olisivat pysyviä, tulee ylimmän johdon ensiksi sitoutua yrityksessä leaniin ja sen johtamiseen. Johtajien tulee ymmärtää, että lean ei konsepti, jonka voi sellaisenaan kopioida suoraan toisesta tehtaasta. Lean on ennen kaikkea tapa toimia jatkuvan parantamisen periaatteiden mukaisesti. Leanillä luodaan kulttuuri, jonka avulla yrityksessä tehdään jatkuvasti pieniä parannuksia ja näin parannetaan yrityksen suorituskykyä.
Lean on tapa toimia. Hukkien vähentäminen on yhteistyötä koko yrityksen sisällä – ei vain yksittäisen osaston tavoite.
Mitä on SMED?
Tutkimustyön metodina käytettiin Shigeo Shingon kehittämää Single Minute Exchange of Die metodia, SMED. Tämä menetelmä etenee systemaattisesti vaihe vaiheelta kohti lyhyempää asetusaikaa. Asetusaika on aika, joka tarvitaan laitteen valmistelemiseen ennen kuin ollaan valmiita aloittamaan uuden tuotteen tai palvelun tekeminen. SMED-menetelmä on käytännönläheinen ja käytettävissä on lukuisia leanin työkaluja, kuten:
- 5S
- spagettidiagrammi
- työvaiheiden standardointi
- juurisyyanalyysit
Usein ajatellaan, että asetusajat vaihtelevat suuresti riippuen käytetystä tuotantolaitteesta, minkä vuoksi jokainen asetusaikaan liittyvä projekti olisi jollain tavalla erilainen. Kuitenkin tarkasteltaessa useammasta eri näkökulmasta, asetusajat voidaan Shingon esittämän teorian mukaan jakaa neljään eri vaiheeseen.
- Sisäisiä ja ulkoisia asetusaikoja ei eroteta toisistaan
- Sisäiset ja ulkoiset asetusajat erotetaan toisistaan
- Sisäiset asetusajat pyritään muuttamaan ulkoisiksi asetusajoiksi
- Tehostetaan kaikkia asetusajan toimintoja.
Saavutetut tulokset
Tutkimustyön tavoitteena oli löytää suurinta hukkaa aiheuttavat tekijät piensäkityslinjalla. Tapaustutkimuksen hukaksi nousi asetusaika.
Saavutetut tulokset olivat:
- Asetusajan lyhentyminen yli 50 %.
- Työvaiheiden vähentyminen 32 vaiheesta 19 työvaiheeseen.
- Kuljettu matka lyheni 343 metristä 199 metriin.
- Aikasäästöä saatiin 39 tuntia vuodessa.
- Vuotuinen säästö on 110 000 €.
Lopetetaan trendiliinaus ja aloitetaan jatkuvan parantamisen kulttuuri ilman yksittäisiä lean työkaluja. Pelkkä 5S työkalun käyttö ei saa riittävää parannusta aikaiseksi. Tarvitaan kokonaisuuden ymmärtämistä ja johtajien sitoutumista parannukseen. Sitouttamalla koko yritys jatkuvan parantamisen kulttuuriin saadaan aikaiseksi pysyviä muutoksia lyhyt kestoisten parannuksien sijaan.
A3-raportti summaa koko projektin kulun pääkohdittain (kuva 1). Tutkimustyön laajuuden vuoksi päädyttiin enemmän visuaaliseen ratkaisuun Likerin seitsemännen periaatteen mukaisesti. Sanotaankin, että yksi kuva kertoo enemmän kuin tuhat sanaa.
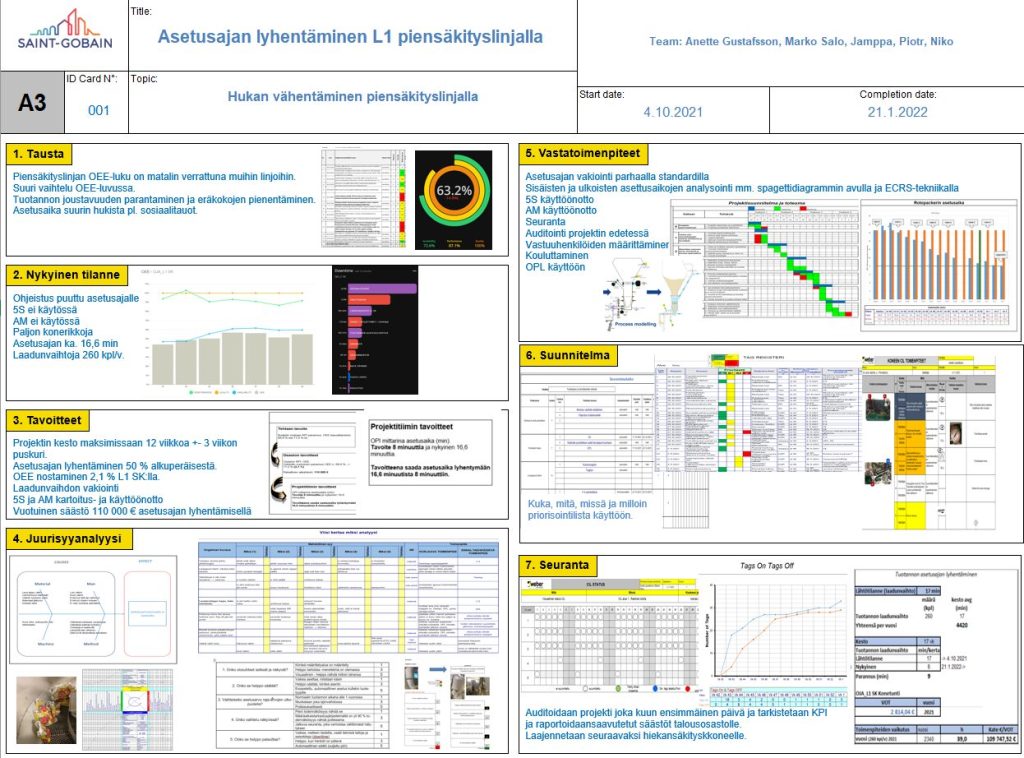
Saavutettujen tuloksien pohjalta uskallankin väittää, että systemaattisesti ja vaihe vaiheelta oikein käytettynä leanillä saadaan tehokkaita tuloksia aikaiseksi.
Tulethan sinäkin mukaan ymmärtämään leaniä syvällisemmin? Lakataan tekemästä niin sanottua trendiliinausta, jossa otetaan käyttöön vain yksittäisiä työkaluja kokonaisuutta ymmärtämättä.
Lähteet
- Gustafsson A. 2022 Hukan vähentäminen (theseus.fi), Turun ammattikorkeakoulun opinnäytetyö
- Liker Jeffrey 2010. Toyotan Tapaan. 3., painos. Suom. Marko Niemi. Helsinki: Readme.fi.
- Liker Jefferey & Convis Gary 2012. Toyotan tapa lean-johtamiseen. Suom. Marko Niemi. Hämeenlinna: Kariston Kirjapaino Oy. Shingo Shigeo 1985. A Revolution in Manufacturing: The SMED System. English translation copyright 1985 by Productivity, Inc.: Cambridge.
- Shingo Shigeo 1986. Zero Quality Control: Source Inspection and the Poka-Yoke System. English translation copyright 1986 by Productivity, Inc.: Cambridge.
- Shingo Shigeo 1989. A Study of the Toyota Production System. Revised Edition, English re-translation copyright 1989 by Productivity, Inc.: Cambridge.